
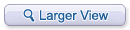
|
The Toyota Way, 14 Management Principles from the World's Greatest Manufacturer (精装)
by Jeffrey K. Liker
Category:
Quality management, Lean production, Process improvement, Corporate transformation |
Market price: ¥ 298.00
MSL price:
¥ 268.00
[ Shop incentives ]
|
Stock:
Pre-order item, lead time 3-7 weeks upon payment [ COD term does not apply to pre-order items ] |
MSL rating:
Good for Gifts
|
MSL Pointer Review:
This is not only an excellent treatise on the Toyota's TPS, but a profound insight on the Kaizen culture, the real core competency of Japanese industries. |
If you want us to help you with the right titles you're looking for, or to make reading recommendations based on your needs, please contact our consultants. |
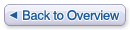
|
|
AllReviews |
1 2  | Total 2 pages 11 items |
|
|
David Mier, USA
<2006-12-22 00:00>
I was one of the first members hired to work in the Toyota manufacturing plant in Kentucky (first 100). As such I was trained by true TPS experts from Japan. I can honestly say that Jeff captures more of the true essence of the Toyota Way than I have ever read. Now I am working with other companies that are attempting to adopt the Toyota philosophies for themselves. It was nice to see information that factually describes the philosophies of Toyota and to be able to share that with these companies.
Unfortunately, some people will read the book and assume that Toyota professes to be (or Liker is professing that they are) perfect. Far from it! Toyota (referring to the leadership of the company) would admit that they have much to improve, and that there are still many opportunities. They do not think they are "lean." In fact, word is that Eiji Toyoda himself said that the book exposed some weakness within Toyota and was an opportunity to reflect on how to become better. This is the true essence of Toyota. Team Member Mike in his review assumes that Liker is suggesting that Toyota is perfect. This is not the case. As with any organization there are many problems. For goodness sake, even though Toyota regularly ranks at the top of the JD Powers quality ranking they still average over 100 problems per vehicle! The notion of greatness is generated from outside of Toyota, not within. The management works hard to stay grounded in reality and certainly is aware of imperfections.
I think this argument is silly and not related to the book. The book is about the philosophy that Toyota embodies to manage their operations. Are there managers that do not live up to the ideal? Of course there are. Does that implicate the entire organization? No, it does not. The book does a good job of illustrating the intention of Toyota as an organization. You may not find here some of the common misunderstandings that are being spread around as "lean manufacturing" because honestly many of those concepts are not based in the Toyota Way.
The results of Toyota speak for themselves. They are outstanding, but not perfect by a long shot. This book does an excellent job of outlining the main concepts, but it would not be possible to outline the entire company with details of how to achieve the results in a single book. It is a very insightful look into a great company, not a blanket praising and blind admiration, but there are many good points about how Toyota intends to operate now and in the future. |
|
|
James Frantz, USA
<2006-12-22 00:00>
When I was hired as a Process Engineer by Toyota and shipped off to Japan to learn how to be a Toyota engineer, I was lucky enough to be a part of the system that Dr. Liker describes in his book. I can, and do, use the text as a guidepost as I look back at the things we did and can better understand the 'Why' versus just the 'What'. The book does an excellent job in laying out a solid structure for the sometimes ethereal concepts within the Toyota Production System and ties them together in a way that is both easy to understand as well as communicate. With this book, we finally have a body of work that transcends the basic Value, Value Stream, Flow, Pull, Perfection framework (don't get me wrong, I strongly support the Womack/Jones framework at operational levels) and gets the reader behind the results and into the thinking processes that drive the behaviors that deliver the results. While some readers that have written in and panned the book seem to think that Dr. Liker is trying to say Toyota is 'perfect', I think that they have, unfortunately, missed the real message in the book. That is too bad for them, because the message is clear and powerful. One respondent sounded like a frustrated UAW organizer, in fact. I can only encourage them to re-read the text and try and gain a deeper understanding of the concepts that are presented. I'm on my sixth reading and the pages are quite dog-eared, sticky noted, and written all over.
Long story short: If you want to get 'into' the thinking processes that drive the most successful automobile company on the planet (can this be disputed?) and begin to apply these processes to your own area, plant, or company, this is the book for you! Let's not forget, Toyota is building a successful business by bringing manufacturing jobs TO America, not rushing headlong to China, India, or some other Asia-Pacific destination. That speaks volumes to the inherent power of Lean to deliver Value to the customer.
|
|
|
An American reader, USA
<2006-12-22 00:00>
I read Dr.Liker's book on Toyota as part of my ongoing research of lean manufacturing. Having read over 2000 articles and various papers on lean, I can say with sufficient impunity that this book gives a deep rooted understanding of the Toyota Way. However, we must take into consideration the views expressed by the team leaders who have been down in the trenches at the Toyota plant; no system is perfect, if it was, it would defeat the purpose of continuous improvement (wouldn't it ?). There is always some gap between theory and practicality, at Toyota they try and keep this gap as little as possible. |
|
|
Victor, USA
<2006-12-22 00:00>
Liker's book is no simple summary of the practices in Toyota's lean toolkit. In fact, he spends a considerable amount of time analyzing the problems U.S. lean sites have encountered when adopting lean tools without fully permeating the principles and philosophies throughout the organization's culture. The examples he cites underline this important deficiency and are worth the price of the book alone.
The chapters on the development of the Lexus and Prius are particularly compelling. Toyota's holistic development approach offers all industries a fine example of how product development should be done. |
|
|
Mark Clarke, USA
<2006-12-22 00:00>
For a person not involved in the manufacturing sector and yet interested in maximizing Church resources especially volunteers and paid ministers the book was thought provoking and insightful. The book's simple and easy to read format help me see ways and opportunities to use this material as I consult with churches and schools. The fourteen steps provided a strong methodology and systematic way of learning and implementing the concepts. Finally, it created a new way of looking at the importance of measurements and how to integrated change into the entire organizational culture. Thanks for the excellent gift to the management literature. |
|
|
Kanishka Sinka, India
<2006-12-22 00:00>
This one fact will sink into your psyche after you read this insightful book - Quality is all about culture
The fourteen principles that you could use as the cornerstone for your organization according to this book (and this particular reviewer) are:
1. Base your management decisions on long term philosophy, even at the expense of short term financial goals
2. Create continuous process flow to bring problems to the surface
3. Use pull systems to avoid over production
4. Level out the workload (Hiejunka)
5. Build a culture of stopping to fix problems to get quality right the first time
6. Standardized tasks are the foundation for continuous improvement and employer empowerment
7. Use visual controls so that no problems are hidden
8. Only use reliable, thoroughly tested technology that serves your people and processes
9. Grow leaders who thoroughly understand the work and live the philosophy
10. Develop exceptional people and teams that follow your company's philosophy
11. Respect your extended network of partners and suppliers by challenging them and helping them improve
12. Go and see for yourself and thoroughly understand the situation (Genchi Genbutsu)
13. Make decisions slowly by consensus thoroughly considering all options. Implement decisions rapidly
14. Become a learning organization through relentless reflection (Hansei) and continuous improvement (Kaizen)
Just an outstanding book. |
|
|
Lars Bergstrom, USA
<2006-12-22 00:00>
This was an excellent book in its own right, focusing on the pillars of excellent that define Toyota's success and discussing how it can or can't be applied to both culturally and technically different fields. The only issue I had with it was the lack of detailed discussions (perhaps because of NDAs?) of what precisely was done to, say, get one-piece-flow in some service organizations. I just had trouble picturing the transformation of machines, people, and services into concrete metrics that justified the work done - and that cuts across most of the examples in the book. While I'm as much of a fan of "facts over metrics" as anybody who is skeptical of statistics, I still like to see some way to measure return on investment or increased efficiency after a rollout is complete.
The bigger benefit, though, is that this book catalogs the root from which a lot of the Lean and Agile work in the software development community has taken its cues. In that conversion to software, some of the fundamental pieces, like jidoka (stopping to fix problems to get quality right the first time) have largely been lost, as have many of the more philosophical principles that supported the long-term success. If you're building your own process cocktail and are already fairly well-versed in Scrum, Crystal, XP, DSDM, and FDD, this is a great book to pick up to make sure you haven't lost some of the overarching philosophy. |
|
|
Charles Cai, USA
<2006-12-22 00:00>
We help companies in USA and Asia implement TPS and Lean manufacturing. This book, now available in Chinese version, has always been the first book we have recommended to our clients. The philosophy of The Toyota Way is the key to assure the success of implementing lean. The 14 management principles Dr. Liker reveals through his tremendous efforts in studying the TPS really teaches you "know why" while many books only teach you "know how". Unless you understand the "know why" and live with it, your lean system is superficial no matter how well you have applied those lean tools, as the author points in the book. For managers in today's competitive global economy, it is worth your time to read this book once, twice and more to learn from the best, The Toyota Way. |
|
|
Leroy Morrow, USA
<2006-12-22 00:00>
The Toyota Way is not about the tools of TPS nor the tools of today's Lean Manufacturing. Dr. Liker wrote and shared with the world the Philosophy the supports and sustains the tools of TPS. It appears that for some who have read Dr. Liker's book that they were expecting for Dr. Liker to have all the reasons for the current operational challenges facing Toyota today. What The Toyota Way speaks to is the philosophy that has placed TMC and their operation systems into the minds of all those individuals that have the current responsibility to make change happen in their current companies. What The Toyota Way truly explains is The Toyota way is more than, Kanbans, Jidoka, Hijunka, A-3s, and all the other TOOLS, it is how an entire organization from top down to bottom up lives and breaths the Philosophy of The Toyota Way. What we in American and I believe it is our manufacturing culture that our current leadership is not in the position to sacrifice short term profitability. Unfortunately our Corporate leaders are measured on the bottom line. Immediate results, today, this month, this quarter, this year, or else. Dr. Liker addresses that Toyota ability to SUSTAIN continual success has been the Philosophy that is The Toyota Way.
Dr. Liker is not to be expected to answer for current operating conditions at TMMK or any other Toyota facility here in North America or any other Toyota facility worldwide. The TMMK team members who have responded to The Toyota Way as missing what is currently happening at TMMK has missed what The Toyota Way is. When I was at TMMK an as an ORIGINAL team member of the startup management team we were taught by our TMC executive coordinators and trainers that if there is a problem then WE all have a problem. No one can be successful if one team member fails. If Toyota, an I speak of Toyota TMC, if they ever came out publicly and shared what has happen to TMMK over the pass 18 years they would admit that they TMC failed to have a stronger input process in the promotion selection. They entrusted the TMMK American Management group to make the selections for promotion and unfortunately to many managers were promoted and they were not trained to be able to meet the required standards to be in that position, mistake one. Mistake two, and this deserves a "traditional" yea but, Toyota was in a period of rapid global expansion and as a result the TMC Executive Coordinators and trainers were spread throughout the world to assist in the global expansion and for a short period TMC took their eyes off of TMMK and as a result of this and a few other things the current conditions that these reviewer of The Toyota Way speak of are the results of what I just mentioned, training and development had been placed on a back burner. Today with the support and commitment of Mr. Cho, Gary Convis is leading the organization through a re-training phase and I know for certain Toyota will be back where it has always been, at the top. It is unfortunate that a current team member of TMMK who is regarded from the outside world as being an expert in TPS today himself does not understand what TPS is nor has he had the opportunity to learn The Toyota Way. I for one and the originals of "TMM", are grateful for Dr. Liker’s book because he captured in his book what we alone were taught by Mr. Cho, Mike Katano, Matt Awazama and what Mr. Gary Convis is currently trying to bring back into standard, The Toyota Way.
If anyone is researching books on the "how to's" of Lean Manufacturing, they found the right web site. If all your looking for are the tools to become lean, Amazon.com is the place to be. If your searching for how do I sustain the tools, how to sustain "values", to your customer, your employee and your community, then you found the right web site to buy the book that will walk you through The Toyota Way. Thank you Dr. Liker, and to Mr. Gary Convis, and the TMM originals. I will share with the world of your pass and current accomplishments and I know that because YOU know what the real secrete is, you know The Toyota Way, even in our slide we know were still the best when compared to the rest and we know we don't compare with the rest, Toyota sets the standard and we just moved the bar up a notch and let the rest play catch up… The secret, The Toyota Way. Read it, believe it, live it.
|
|
|
Larry Simpson, USA
<2006-12-22 00:00>
I recently had a senior executive in my company send me a template for what was labeled an "A-3 form". He said he wanted all his managers to use the form to map out their proposed projects and processes. He suggested that we buy a copy of Jeffrey Liker's book to understand it's basis. I bought and read the book, and found Chapters 13 & 14 particularly helpful in understanding the need and purpose for such a form. It provided some detailed insight on how to complete the form in a way that it best serves its purpose. It explained and illustrated the some of the less intuitive aspects such as the "root cause analysis". Although the book showed the A-3 document in a format labeled PDCA (Plan-Do-Check-Act) and the Toyota form actually sent from my boss was labeled (Plan-Do-Learn), the contents were essentially the same. For anyone wanting to better visualize their processes and projects quicker, I highly recommend this book to see how Toyota has successfully applied "a picture is worth a thousand words" to their standardized reporting procedure. |
|
|
|
1 2  | Total 2 pages 11 items |
|
|
|
|
|
|