
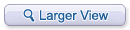
|
Lean Thinking : Banish Waste and Create Wealth in Your Corporation, Revised and Updated (Audio CD)
by James P. Womack, Daniel Jones
Category:
Lean thinking, Six Sigma, Productivity improvement |
Market price: ¥ 328.00
MSL price:
¥ 298.00
[ Shop incentives ]
|
Stock:
Pre-order item, lead time 3-7 weeks upon payment [ COD term does not apply to pre-order items ] |
|
MSL rating:
Good for Gifts
|
MSL Pointer Review:
A good introduction to and an real world application source of Lean Production, this book will help the redesign of business when everyone is aware Toyota will soon displace GM as the world's biggest automaker. |
If you want us to help you with the right titles you're looking for, or to make reading recommendations based on your needs, please contact our consultants. |
 Detail |
 Author |
 Description |
 Excerpt |
 Reviews |
|
|
Author: James P. Womack, Daniel Jones
Publisher: Simon & Schuster Audio; Exp Upd edition
Pub. in: June, 2003
ISBN: 0743530489
Pages:
Measurements: 5.9 x 5 x 1 inches
Origin of product: USA
Order code: BB00069
Other information: Reprint edition ISBN-13: 978-0743530484
|
Rate this product:
|
- Awards & Credential -
One of the best guides to the principles and practices of Lean Production and Toyota Production System (TPS). |
- MSL Picks -
Lean thinking shift management concern away from assets and finance and focuses them on the perspective of the customer. Value is provided when the supplier gives the customer exactly what they want when they want it and the producer creates value. Lean thinking provides immediate value by converting waste into value. Value is a conscious attempt to precisely define value in terms of a specific product with specific capabilities at a specific price through a dialogue with the customer. Managers need to rethink along product line and not existing assets and technologies.
The value stream has three components: 1. the problem solving task 2. Information management 3. and transformation task. The value stream exposes and finds many steps that create no value and should be immediately avoidable. How does so much waste occur for such a long time? The departments or parties are not accountable nor forced to explain their products, processes, or service to others. Secondly, there exists the matter of confidentiality where non-disclosure creates barriers and artificial dependency. Third, the matter of the obvious circumvents the desire to continual improve and reexamine process and product.
Value stream begins with "one thing at a time" as more efficient than batch processing. Batch processing is the culture of the farmer. The farmer culture has replaced the hunter culture. The hunter culture is more efficient, as it seeks to "build what the customer wants when the customer wants it" or in other words "on-demand production". On-demand production destroys the need for forecasting and lets the customer pull the product from the product when needed. Lean thinking cuts production through times by 90% and reduces inventories by 90%. Batch processing or mass production thinking results in stagnation which leads to cost cutting, an innovation incentive killer.
Lean thinking starts with analysis of flow. The manufacturing process is divided into cells. Each cell represents one or more sequence of assembly and transformation processes. A tub is passed between each cell and triggers a series of events to start in the cell. The parts associated with the tub are built exactly and immediately. Any process or resource that does not contribute value in the flow is removed. Higher demand cells are place at the beginning of the flow. Cells can be run in parallel creating economy of scale load balancing. A critical failure can stop all the production. Quality teams constant analyze the flow for defect and workers in the cell are allowed to respond and communicate problems and suggestions for improvement.
Lean thinking begins with pull. Customers pull products from the producer and remove the need for forecasting and excessive inventories size. Machines are equipped with fast transforming technology allowing for a diverse combination of assembled options for parts and products moving from cell to cell. Lean thinking is better than MRP. Lean thinking removes the slack time in scheduling errors and miscalculations in forecasted quantity amounts and types.
Lean thinking must be applied to all aspects of product creation and delivery. Lean thinking removes any flow issues associated with getting the correct product to the customer, quickly, accurately, and efficiently. Lean thinking replaces mass production process engineering and exposes process weakness and factories have tolerated and managed these failures as a part of the mass production cycles. Lean product exposes these weaknesses and replaces them with more feasible solutions.
Manufacturing Perfection is impossible, however thinking about perfection leads to inspiration and innovative solutions. Lean thinkers bring abundance to the market, transform nonstandard products into standardized products, and increase customer value. The value of lean thinking is continuous improvement in quality, design, and product.
(From quoting D. Nishimoto, USA)
Target readers:
Executives, managers, entrepreneurs, engineers, operations leaders, management consultants, Lean Production trainers, MBAs, government leaders, and professionals.
|
James Womack and Daniel Jones have collaborated on analyses of global industrial trends for more than twenty years. They are coauthors of The Machine That Changed the World, Seeing the Whole, and The Future of the Automobile.
Womack is founder and president of the Lean Enterprise Institute (www.lean.org), a nonprofit education and research organization based in Brookline, Massachusetts, dedicated to the spread of lean thinking.
Jones is founder and chairman of the Lean Enterprise Academy in the U.K. (www.leanuk.org), a nonprofit organization affiliated with the Lean Enterprise Institute and pursuing the same objectives in English-speaking Europe.
|
From Publisher
Expanded, updated, and more relevant than ever, this bestselling business classic by two internationally renowned management analysts describes a business system for the twenty-first century that supersedes the mass production system of Ford, the financial control system of Sloan, and the strategic system of Welch and GE. It is based on the Toyota (lean) model, which combines operational excellence with value-based strategies to produce steady growth through a wide range of economic conditions.
In contrast with the crash-and-burn performance of companies trumpeted by business gurus in the 1990s, the firms profiled in Lean Thinking - from tiny Lantech to midsized Wiremold to niche producer Porsche to gigantic Pratt & Whitney - have kept on keeping on, largely unnoticed, along a steady upward path through the market turbulence and crushed dreams of the early twenty-first century. Meanwhile, the leader in lean thinking - Toyota - has set its sights on leadership of the global motor vehicle industry in this decade.
Instead of constantly reinventing business models, lean thinkers go back to basics by asking what the customer really perceives as value. (It's often not at all what existing organizations and assets would suggest.) The next step is to line up value-creating activities for a specific product along a value stream while eliminating activities (usually the majority) that don't add value. Then the lean thinker creates a flow condition in which the design and the product advance smoothly and rapidly at the pull of the customer (rather than the push of the producer). Finally, as flow and pull are implemented, the lean thinker speeds up the cycle of improvement in pursuit of perfection. The first part of this book describes each of these concepts and makes them come alive with striking examples.
Lean Thinking clearly demonstrates that these simple ideas can breathe new life into any company in any industry in any country. But most managers need guidance on how to make the lean leap in their firm. Part II provides a step-by-step action plan, based on in-depth studies of more than fifty lean companies in a wide range of industries across the world.
Even those readers who believe they have embraced lean thinking will discover in Part III that another dramatic leap is possible by creating an extended lean enterprise for each of their product families that tightly links value-creating activities from raw materials to customer.
In Part IV, an epilogue to the original edition, the story of lean thinking is brought up-to-date with an enhanced action plan based on the experiences of a range of lean firms since the original publication of Lean Thinking.
Lean Thinking does not provide a new management "program" for the one-minute manager. Instead, it offers a new method of thinking, of being, and, above all, of doing for the serious long-term manager - a method that is changing the world.
|
Chapter 1
Value
A House or a Hassle-Free Experience?
Doyle Wilson of Austin, Texas, had been building homes for fifteen years before he got serious about quality. "In October of 1991 I just got disgusted. Such a large part of my business was waiting and rework, with expensive warranty claims and friction with customers, that I knew there must be a better way. Then I stumbled across the quality movement."
He read Carl Sewell's book on car dealing, Customers for Life, and decided to test his claims by buying a car at Sewell's Dallas dealership. ("I thought that if even a car dealer could make a customer feel good, it should be easy for a homebuilder!") His purchase was such a positive experience that he asked Sewell for advice on quality in home building and was told to read the works of W. Edwards Deming.
Doyle Wilson is the archetypical Texan and never does things halfway. By February of 1992 he had launched a wall-to-wall Total Quality Management campaign at Doyle Wilson Homebuilder. Over the next three years he personally taught his workforce the principles of TQM, began to collect and analyze enormous amounts of data on every aspect of his business, got rid of individual sales commissions ("which destroy quality consciousness"), eliminated the traditional "builder bonus" for his construction superintendents (who were qualifying for the "on-time completion" bonus by making side deals with customers on a "to-be-done-later" list), reduced his contractor corps by two thirds, and required the remaining contractors to attend (and pay for) his monthly quality seminars.
Customer surveys showed a steady rise in satisfaction with the homebuilding experience and sales grew steadily even in a fiat market as Wilson took sales from his competitors. In 1995, Doyle Wilson Homebuilder won the National Housing Quality Award (often called the Baldrige Award for quality of the construction industry), and Wilson set a goal of winning the Baldrige Award itself by 1998. Yet he was not satisfied.
"I knew I was making progress in competing with other builders for the new-home buyer, but a simple fact, once it lodged in my mind, wouldn't go away: 78 percent of the homes bought in central Texas each year are 'used' or older homes. I've been making progress in increasing my share of the 22 percent seeking a new home, but what about the 78 percent who bought older homes? Obviously, these buyers are the real market opportunity."
So instead of surveying people who were buying new homes, Wilson began to talk with people who were buying older homes. What he discovered was obvious in retrospect but has required a complete rethinking of his business. Specifically, he found that many buyers of older homes hated the "hassle factor" in negotiating for new construction, the long lead times to get the job done and move in, the inevitable "to-be-done" list after moving in, and the "phony choices" available from builders who promise custom homes but then load on as "standard equipment" many features of little interest to buyers.
Wilson soon realized that that was exactly what he had been asking his customers to go through. By contrast, older-home customers could clearly see what they were getting, buy only what they wanted, and, often, move in immediately. "No wonder I was losing 78 percent of my potential customers!"
To create a hassle-free experience to go with the house itself (these together constituting Wilson's "product"), it was necessary to rethink every step in the process. He has recently opened a one-stop sales center where the customer can see and decide on every option available in a house (for example, the forty different varieties of brick, the three thousand varieties of wallpaper, the four styles of built-in home office), customize a basic design with the help of an Auto-Cad computer system, select features beyond the standard level (for example, extra-thick carpet pads, additional outdoor lighting, and heavier-duty wiring), determine the exact price, work out the mortgage, arrange for insurance, and arrange for the title search. For customers truly in a hurry this can be done during one walk-through of the sales center.
To shrink the lead time from contract signing to moving in from six months to a target of thirty days, he has reorganized his contract-writing and job-release process and is developing a system of pull scheduling for contractors who are assigned new jobs as downstream jobs are completed.
He is also introducing standardized work statements, parts lists, and tool kits for every job. Eventually these steps will eliminate the "to-do" list because the new system does not allow the next task to start until the previous task is certified as complete with perfect quality.
Finally, Wilson has created a wide range of basic house designs with a minimum construction standard and asks the customer to specify all materials and systems upgrades (using the computer design system) to a selected base design so the customer only pays for exactly what she or he feels is really needed.
Doing all of this will not be easy, as we'll see when we return to this example in Chapter 3 on fiow, but Doyle Wilson has already made the key leap. Instead of concentrating on conventional markets and what he and his contractors were accustomed to making in a conventional way, he has looked hard at value as defined by his customers and set off down a new path.
Start by Challenging Traditional Definitions of "Value"
Why is it so hard to start at the right place, to correctly define value? Partly because most producers want to make what they are already making and partly because many customers only know how to ask for some variant of what they are already getting. They simply start in the wrong place and end up at the wrong destination. Then, when providers or customers do decide to rethink value, they often fall back on simple formulas - lower cost, increased product variety through customization, instant delivery - rather than jointly analyzing value and challenging old definitions to see what's really needed.
Steve Maynard, vice president for engineering and product development at the Wiremold Company in West Hartford, Connecticut, was trying to deal with these very problems when he reorganized Wiremold's product development system in 1992. For many years previously, Wiremold had developed new products - consisting of wire guides for office and industrial users and surge protectors for PCs and other business electronics - through a conventional departmentalized process. It started with marketing, which commissioned surveys comparing Wiremold's products with the offerings of competitors. When an "opportunity" was identified, usually a gap in the market or a reported weakness in a competitor's offering, a design was developed by product engineering, then tested by the prototype group. If it worked according to specification, the design proceeded to the engineers designing the machines to make the products and eventually went into production.
This system produced designs which lacked imagination and which customers often ignored. (The designs also took too much time and effort to develop and cost too much to make, but these are a different type of problem we'll discuss in Chapter 3.) Simply speeding up this process through simultaneous engineering and then broadening product variety would just have brought more bad designs to market faster. Pure muda.
Steve Maynard's solution was to form a team for each product to stick with that product during its entire production life. This team - consisting of a marketer, a product engineer, and a tooling/process engineer - proceeded to enter into a dialogue with leading customers (major contractors) in which all of the old products and solutions were ignored. Instead, the customer and the producer (Wiremold) focused on the value the customer really needed.
For example, traditional Wiremold wire guides (which channel wiring through hostile factory environments and provide complex arrays of outlets in high-use areas like laboratories and hospitals) had been designed almost entirely with regard to their ruggedness, safety, and cost per foot as delivered to the construction site. This approach nicely matched the mentality of Wiremold's product engineers, who dominated the development process and who found a narrow, "specification" focus very reassuring.
As the new dialogue began, it quickly developed that what customers also wanted was a product that "looked nice" and could be installed at the construction site very quickly. (Wiremold had never employed a stylist and knew relatively little about trends in the construction process.) Customers were willing to make substantial trades on cost per foot to get better appearance (which increased the bid price of construction jobs) and quicker installation (which reduced total cost).
Within two years, as all of Wiremold's product families were given the team treatment, sales for these very conventional products increased by more than 40 percent and gross margins soared. Starting over with a joint customer-producer dialogue on value paid a major dividend for Wiremold quite aside from savings in product development and production costs.
While Wiremold and Doyle Wilson Homebuilder and every other firm needs to be searching for fundamentally new capabilities that will permit them to create value in unimagined dimensions, most firms can substantially boost sales immediately if they find a mechanism for rethinking the value of their core products to their customers...
|
|
View all 9 comments |
Fortune (MSL quote), USA
<2007-01-31 00:00>
A new and coherent thesis about automotive production... [the authors] back up their conclusions with unique statistical measures that are authoritative, extremely timely, and highly revealing. Think of this book as another step in the decade-long process of getting the attention of recalcitrant mass producers. |
David Rouse (Booklist) (MSL quote), USA
<2007-01-31 00:00>
In The Machine That Changed the World (1990), Womack and Jones, along with Daniel Roos, lauded the manufacturing technique used by Japanese automakers, known as "lean production" and also as the Toyota Production System. Lately, though, some critics have argued that "lean production" has been used as simply an excuse for downsizing, and recent books, such as David Gordon's Fat and Mean (1996), have questioned whether corporate trimming has been effective at all. Undaunted, Womack and Jones argue their case anew. They now move beyond "lean production" to propose "the lean enterprise" and describe the successes at 25 U.S., Japanese, and German companies that have effectively implemented the "lean principles" of value (as defined by the customer), value stream, flow, pull, and perfection. Because their earlier book has sold well, this follow-up could generate interest. |
Robert Morris (MSL quote), USA
<2007-01-31 00:00>
This is a new and expanded second edition of a book first published in 1996. Of special interest to me was what Womack and Jones had to say in the preface regarding what has since happened to the companies previously discussed. Apparently lean thinking has enabled Toyota, Wiremold, Porsche, Lantech, and Pratt & Whitney to sustain operational excellence and economic prosperity.
Briefly, how do Womack and Jones define lean thinking? It is the opposite of muda (a Japanese) word for anything which consumes resources without creating value. In a word, waste. Lean thinking is lean because "it provides a way to do more and more with less and less - less human effort, less equipment, less time, and less space - while coming closer and closer to providing customers with exactly what they want." Lean thinking is thus a process of thought, not an expedient response or a stop-gap solution. The challenge, according to Womack and Jones, is to convert muda into real, quantifiable value and the process to achieve that worthy objective requires everyone within an organization (regardless of size or nature) to be actively involved in that process. Once again, in this new edition they address questions such as these:
1. How can certain "simple, actionable principles" enable any business to create lasting value during any business conditions?
2. How can these principles be applied most effectively in real businesses, regardless of size or nature?
3. How can a relentless focus on the value stream for every product create "a true lean enterprise that optimizes the value created for the customer while minimizing time, cost, and errors"?
In Part IV, Womack and Jones update the continuing advance of of lean thinking. They rack the trend in inventory turns and the progress of their profiled companies. Also of special interest to me was the discussion of what Womack and Jones have learned since 1996 which probably explains why they introduce a new range of implementation tools support value stream mapping initiatives and thereby "to raise consciousness about value and its components, leading to action."
Obviously, even if everyone involved within a given organization is committed to lean thinking, to creating value while (and by) eliminating waste, the process requires specific strategies and tactics to succeed. Hence the importance of the last chapter in this book., "Institutionalizing the Revolution." I presume to suggest that the process of lean thinking never ends. Inevitably, success creates abundance; abundance often permits waste. I also presume to suggest that priorities must first be set so that the implementation of lean thinking process does not inadvertently create or neglect waste in areas which influence the creation of value for customers.
Although highly readable, this is not an "easy read" because it requires rigorous thinking about what is most important to a given organization, rigorous thinking about the root causes (rather than the symptoms) of that organization's problems, and rigorous thinking about the most prudent use of resources to eliminate those problems. Because of the importance of the material which Womack and Jones share, I strongly recommend that decision-makers read and then re-read this book before getting together to exchange reactions to it. Out of that discussion, I hope, will come both a collective commitment to lean thinking and the personal determination of each executive to apply what she or he has learned from this book in operational areas where waste has most diminished value.
|
Rolf Dobelli (MSL quote), Switzerland
<2007-01-31 00:00>
James P. Womack and Daniel T. Jones sound a battle cry against institutional waste. What a pity, they say, that so much time, energy, and money are needlessly thrown away. They urge executives to redefine their values based on customer experiences and to track the flow of value from manufacturing to final sale. The result, they promise, is that companies will save time, energy and money - and will revolutionize their entire organizations in the bargain. Not content to simply study western problem-solving methods, the worldly authors guide their readers through a wide array of Japanese manufacturing wisdom as well. Their generosity and depth make this a pleasantly informative book, which defies the current trend in business books of proclaiming doom and then offering a quick fix. This book would rather proclaim hope, which is just one of the reasons that we [...] recommend it to serious managers who want to trim the fat.
|
View all 9 comments |
|
|
|
|